Operations may be slow now, but will ramp-up again sooner or later.
Very unusual circumstances caused the shut-down and the recovery will probably be also.
At Pinqkerton, our closest experience (from a previous life), to what we might be living soon, is a process transfer from one location to another. Based on that experience, we believe that this recovery will require a good dose of planning but is an opportunity to learn and progress.
In the case of a process transfer, most of the start-up (i.e. the recovery) at the receiving end depends on the shut-down and transfer of knowledge.
The differences with today are (i) this shut down was potentially organized in a bit of a rush (ii) the process understanding that was not developed before the shut down will not be available for the recovery.
We hope the experiences, information and advices collected from various sources (mainly from the food industry) and shared hereafter will provide you with at least one actionable idea that will help you recover faster and better.
So we start with an evaluation of the process state after shut down and quarantine, what we know about it and build the knowledge that is missing.
What do companies who go through seasonal shut-down pay attention to ?
A shut-down has a number of consequences:
- Water stops circulating : its quality drops
That can be a concern since water is used among other things, for cleaning - Wet areas : humidity, condensation, residual water .. lead to microbial proliferation and development of biofilms
72h is often used as a reference in the food industry as an action limit to trigger a re-washing. (max 24h is a target) - Dry areas : crusting takes place and standard washes are not enough to remove them
Remaining crust will act as a anchor for new biofilm or other contamination - Pests : the facility has known unusual calm for an unusual long time and unusual visitors can be expected
- Dryness damages seals or other parts…
- Humidity favors contamination of the air system, vents…
- Uncontrolled temperature leads to premature material aging, spoilage…
Good shut down practices in seasonal farming suggest measures that are generic and important for their restart. They include:
- Empty/ purge all lines and containers
- Apply the most thorough cleaning procedures e.g. alkali wash followed by acid rinse.If possible: allow to dry and close or leave in a protective solution e.g. peracetic acid
- Close all networks (compressed air, water, CO2, etc.)
- Disassemble all equipment that can be, prior to inspection and washing : unions, filter housings, heat-exchangers, etc
- Scrub all accessible surfaces, including inside vats and silos, in safe conditions.
- Isolate and close packages of started materials, (if possible, put under vacuum)
- Close the drains to avoid the rise of contaminating microorganisms
- Install grids to avoid the rise or entry of rodents
- Take stock and prevent looting / burglaries
If these steps were not taken during shut-down, they could or should be during recovery.
What do we know that is important for recovery ?
We know at least 2 things that are important: the process and the product susceptibility to contamination, the combination of which is reflected in the historical production yields and/or spoiled batches.
Hygiene by Design dictates that the exterior and interior of all equipment and pipework must be self-draining or drainable. In the case of external surfaces, any liquid must be directed away from the main product area. The design rules include choice of material of construction and other sometimes industry-specific considerations.
Some of our conception flaws can be detected by observation, such as areas of water stagnation which point at potential vulnerabilities to contamination.
Now is the opportunity to look, discover and improve.
Then, we also have our production history as a source of information.The documentation and/or personal experience tell us which intermediate or finished product, which particular tank, supplier or process step has been most problematic.
If those production pain points present a higher risk of contamination in normal conditions, they probably hurt even more during recovery.
We can think of actions such as re-inforced inspection, avoidance (recover with manufacturing other « easier » products first, before manufacturing the more complicated ones) or upgrade the process.
This last option, in our experience, should be considered with care because of 2 conflicting propositions:
- First, if we have a known weak point in a chain and we know times ahead will be challenging, then dealing with the weak point might well increase our chances of success. It is good preparation.
- On the other hand adding change to a crisis situation, when resources are spread thin and thinking clear not easy, could bring the entire organisation to a stop if anything unexpected happens. It is taking unnecessary risk.
The decision might be taken considering a « risk/benefit » ratio, return on investment and our capacity to do it right the first time?
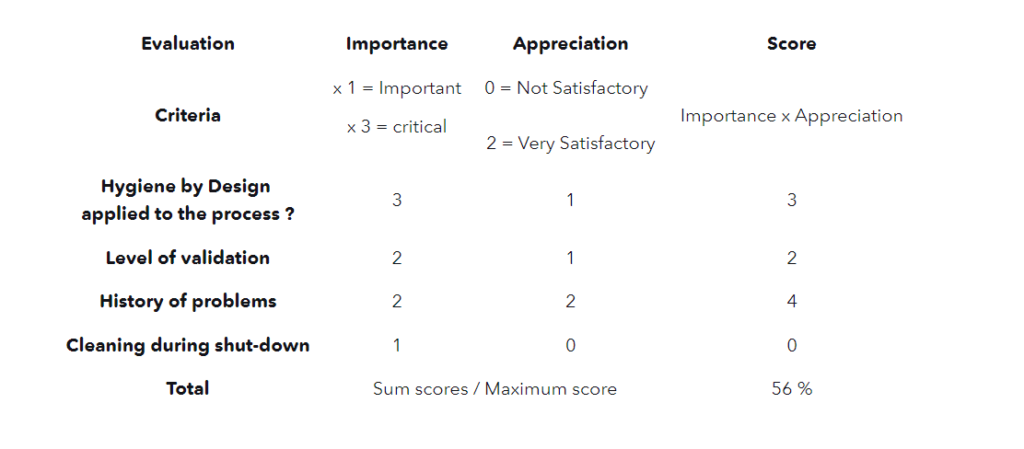
Everything in this table is up for customisation, including the granularity for the criteria and evaluations. It may facilitate an assessment that can be explained, shared and feed a plan for recovery. A more comprehensive version can also be the starting point for a longer term Operational RoadMap, with annual objectives to improve the score.
How do we know we have recovered ?
For those processes and procedures that are validated, the key performance indicators are known, acceptable limits are specified etc.
Re-start could look like a walk in the park (relatively)
The answer to that question is made more difficult when we have insufficient or partial data history. If we don’t have measures or specifications to indicate what normal/satisfactory/improved are, we can remember Peter Drucker : “If you can’t measure it, you can’t improve it »
The missing historical data can be built on this occasion.
Before the actual restart, we can test critical control points, points-of-use, water at various purification and storage steps, etc. which will give a reference point helpful to evaluate the efficiency of the cleaning and other recovery activities.
Chances are, that data will come useful again, and again for years to come
Preaching one second for our products: the nomad testers can really come handy in these circumstances.
A few points of attention
- Recent public debriefs from companies that have managed to function through this confinement period, one in Food and the other in PCP, both highlighted the importance of communication.
Their point is that for a group to function in unusual conditions, everyone needs more than ever to be and feel listened to, considered and be lead rather than managed.
In these experiences, the energy and creativity that were liberated really made the difference.
- Those large companies also had a wealth of experience and documentation i.e. a large toolbox from which they could draw. Here are some we thought might be helpful:
- Beware of washing on biofilms or dry crusts well installed: start washing with a cold phase to remove organic and especially protein residues which hot coagulate on the walls and are very difficult to remove, and then form points of hook for subsequent deposits and biofilms.
- Watch out for air systems, air intakes and introduction into the process.
- Monitor fines (dust of various origins which are vectors of cross-contamination of the environment between zones ) in the workshops. Where are these fines generated? where do they circulate?
Places where fines deposit risk harboring contaminations that might adapt, become resistant to the sanitation process,particulalrly in process dead-points. - Are there any plans to rework rework? how was it stored? Where will the rework be introduced in the process?
- Atmospheres: has the temperature been lowered? Was it only when everything was dry? Has there potentially been any condensations?
- A scrupulous inspection is necessary before restarting
In many cases, visual inspections are the main or only way to check that a particular criteria is met, even in normal activities.
Training new personnel or standardizing the acceptable limits is not always simple for those visual controls. For that purpose, building a library of different defects, labelled « acceptable » or « not » can be very useful. `
There are rare occasions to enrich these libraries and a restart is probably one of them.
We find that taking pictures with smartphone is a smart way of doing that. It does not cost much and can prove very valuable
- Gather data
An unusually high level of testing might be desirable to satisfy yourself and potential auditors that the process is back under control.
In case of sensitive materials and or processes, swabs will be necessary if only to measure TVC (Total Viable Counts) and a few hygiene process specific indicators, at sensitive points identified during an inspection before recovery.
Same goes for equipment rinse water for equipment internal surfaces.
Identification of the germs found would allow the use of cleaning agents well targeted for their specific efficacy and at the effective dose as well as doing some plant mapping.
Mapping is helpful to determine the origin and movements of contaminants in a site. If we know what flora is in the process water, what is typically from a raw material, and another form the skin, when we find a contamination in a product, the origin of the contamination is easier to investigate.
This approach applied in routine can be a luxury for some activities, as a result of (i) the testing costs being to high compared to the product value and (ii) because the results of swabs or CIP rinse water test (before second washing and possibly post second washing), would not be known until after the manufacturing has resumed. The delayed results may expose to a difficult decision : what if a troubling result is found in retrospect, after the manufacturing restart, that is not part of the release criteria ?
For that reason maybe, some manufacturers consider that the first batch, scrutinized, should be discarded no matter what.
But such an approach might be acceptable in a recovery “study” mode during the upcoming start-up, to enhance our process understanding, which is a source of lasting future improvements and savings.
Where are the opportunities in all that ?
As a supply chain management expert pointed out this week, that we are living an opportunity to improve in a number of ways:
- Financially: because cash is priority number 1 right now, short term profitability left aside, if we look at our activity focussed only on current and future cash-flows, we may reveal improvements: contracting the supply chain, resizing batches and equipment, reconsider the value of a particular sales channel or customer type
- Sales : some companies will probably not survive through this death valley unfortunately, which opens new markets for those who survive
- Organisation : observe the time between taking important decisions and their realisation.
What is slowing the process: communications, planning, adapting operations, lack of automation ? - Strategic : developing agility and resilience.
What is our process for anticipation and decision making. How does it work when our vision of the future is not clear ?
The post crisis consumer habits, behavior at work, economic models might be different : place bets on a few scenarios, prepare a response and pull the trigger when one of the bets becomes reality
Conclusion
Several executives from reputable companies converge in the opinion that recovery is an opportunity to become more agile and resilient.
This is consistent with our experience in process transfers.
It starts with observing our processes, organisation and cash-flows to identify vulnerabilities. It continues with anticipating, adapting while measuring the progress.
It may sound as the kind of conceptual thinking exclusive of large companies, but are these opportunities not real for all companies, whatever size and business ?
Like for exceptional holidays, these exceptional days call for observing, taking pictures, comparing, so we can bring new habits and ideas home, on which to feed for a long time.Thank you for reading this.
If you would like more publications like this one, please “Like” or comment.
We’d love to read from you, share and help !
As a token of our appreciation, enjoy free shipping on our products, with the code ILIKEBLOG4
…and remember,
Q: Why did the germ cross the microscope ?
A: To get to the other slide !