A complex water purification system set to spec for custom products
In this case, we are looking at an incident at ProTek (name changed for the confidentiality of the business), a Biotech CRO company which produces a diverse range of small production batches set to customer specifications.
To fulfill orders, ProTek makes wide use of purified water in the process, and also as a component of the final product.
The ProTek production system is advanced, capable of delivering highly purified water at 9 points of use via a recirculation loop. The purification train includes a softener, filtration, reverse osmosis, electrodeionization, a 0,22um vent filtered tank feeding a recirculation loop with an online 0,2um membrane filtration step.
The entire system is decontaminated monthly with a caustic and hydrogen peroxide solution then rinsed until pH approaches 7.
ProTek monitors the system parameters (resistivity, RO rejection, etc.), but no microbial tests are performed.
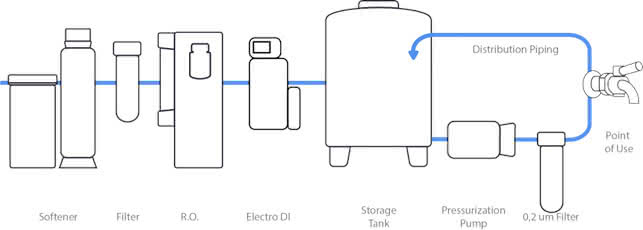
One of ProTek’s products has a specification for low levels of pyrogens. Microbial pyrogens are produced by bacteria, some of which can form hard-to-remove biofilms on surfaces. Since water is the biggest potential contributor to microbial pyrogens, ProTek was controlling water quality prior to processing with a portable rapid endotoxin detection system supplied commercially from a leading company.
Unacceptable pyrogen levels in the system start recurring
One Monday, a ProTek employee noticed a pyrogen result for the water at the point of use was OOS (Out-of-Specification).
To identify the source of the contamination, pyrogen tests were performed at other sampling points, including the tank outlet, the DI outlet, the RO system. Results were within spec for all sampling points, except for the storage tank, making it the primary suspect.
ProTek halted production, decontaminated and rinsed the system, giving time for the storage tank to refill and for the water quality to be controlled again.
Pyrogen levels were back within specification, but the batch was processed 24 hours behind schedule, putting pressure on the downstream operations to be completed that week.
2 weeks later, before the processing of another product with similar pyrogen requirements, test results showed a new contamination event, with excessive levels of pyrogens.
The same curative measures were implemented before production could be resumed.
Investigating to find the root cause of recontamination
When water quality is OOS, the batch in production is processed with a delay of 24 hours, which puts pressure on downstream operations.
- An investigation needed to identify the root cause of the recurring contamination. Then a preventative measure needed to be implemented and checked for effectiveness.
- ProTek lacked appropriate microbial monitoring devices and techniques. In addition, the paper lab book for the maintenance of the water system was stored in the technical room, far from where samples were actually being analyzed. For a practical and effective solution, stand-alone devices and some form of data management system were required to collect and analyze the data.
Systematic and risk-based approaches to the investigation
The investigation plan involved microbial testing of various points:
- those perceived as being potential sources of contamination (a risk-based approach)
- those found at each important step of the purification and distribution system (a systematic approach)
- distributed at a frequency suitable to identify variations in the sanitary conditions of the system
A sampling plan to hunt down the source
The sampling plan established:
- the tank feed water and stored water every 2 days
- water from the last point of use on the recirculation loop
- loop feedback water
- on a schedule set for several times per week, to cover the different configurations, e.g. at start-up on Monday after 2 days without use, and at the end of the week after repeated contacts with the points of use
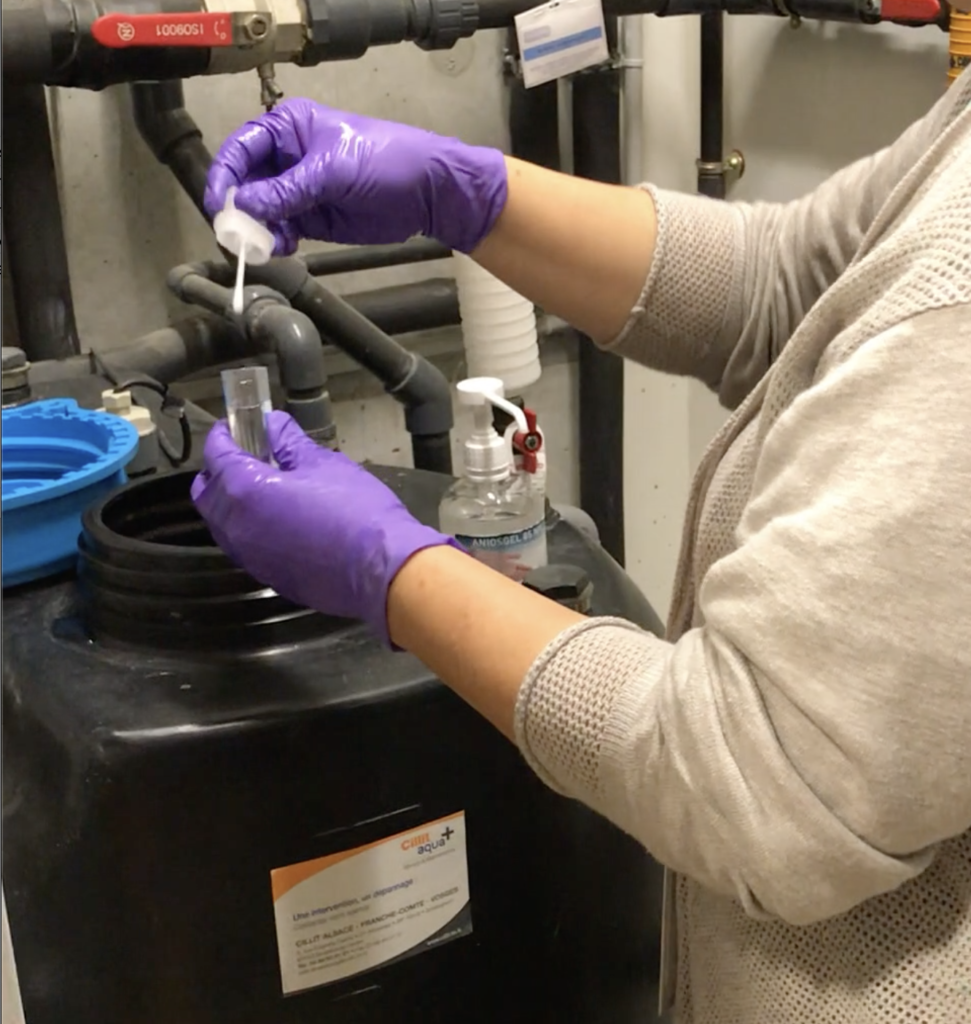
Due to a lack of appropriate microbiology capabilities, the investigation was conducted using a pyrogen detection device. This solution is expensive and not ideal, since pyrogens (lipopolysaccharides) are produced only by gram negative bacteria such as pseudomonas, but not micrococcus, hence the results did not reflect the total microbial population in the water.
A biofilm revealed as the cause of recontamination
ProTek’s investigation was conducted over the course of a couple of weeks until the prime suspect was identified:
- Findings during that period suggested that microbial levels could dramatically increase after a period as short as 3-5 days after full decontamination
- The prime suspect was identified during testing of the loop feedback water which was sampled from within the tank through the manhole. On one occasion, it was noted that portions of the tank sealing were viscous to the touch. Surface sampling of the sealing and consequent testing confirmed that a biofilm had developed, suspended over the purified water, and regularly dropping into it.
A problem managed and a monitoring program for the future
As a result of the investigation, the following control measures were implemented:
- a UV lamp was added inside the tank
- decontaminations began to be conducted with the tank full to the overflow outlet
- a schedule for regular controls of the tank with a quantitative microbiology technique, up to once a week in the summer, was established and recorded on the system logbook for monitoring and trend analysis
The measures and control plan were effective in preventing the reoccurrence of the contamination problem, allowing ProTek to avoid further setbacks in its production schedule.
Humidity and protection from contact with santitants allowed microbes to flourish
A biofilm in the storage tank was the cause of the recontamination.
How did it form in the first place?
- The sealing was constantly humid, due in part to condensation, but in majority due to the splashes caused by the feedback water from the top of the tank falling onto the water surface. A constantly humid surface is a good support for biofilms to take hold and grow.
- The surface was not decontaminated/sanitized:
Decontamination procedures with caustic and Hydrogen Peroxyde is only effective on surfaces in contact for some time with the sanitizing solution. In this system set-up, the incriminated surface was not effectively decontaminated.
Insights:
- This case is a reminder that water supports life: give them even a small chance and microorganisms will grow when there is water, even in small amounts, and so properly drying equipment (when possible) and ensuring full contact of sanitants with all humid surfaces are important for hygiene
Other troubling spots to keep an eye on
The insights from ProTek’s case may alert us to other equipment for which complete sanitization or drying may be difficult and open the door to contaminations:
- neck rest seals from bottling equipment
- storage tanks without a sprinkler ball for sanitation
- plant floors difficult to access with a squeegee
Microbe-wise – A quick look at Pseudomonas aeruginosa
Pseudomonas aeruginosa is a common gram-negative bacterium that can cause disease in plants and animals, including humans.
It is found in soil, water, skin flora, and most man-made environments throughout the world. It thrives not only in normal atmospheres, but also in low-oxygen atmospheres, thus has colonized many natural and artificial environments. Because it thrives on moist surfaces, this bacterium is also found on and in medical equipment, including catheters, causing cross-infections in hospitals and clinics. It is also able to decompose hydrocarbons and has been used to break down tarballs and oil from oil spills. P. aeruginosa is not extremely virulent in comparison with other major pathogenic bacterial species but is capable of extensive colonization, and can aggregate into enduring biofilms.

Disclaimers
This Use Case is based on a true story! (Though we edited it for readability and, of course, for confidentiality.) We like to tell stories about real situations because we think they help translate raw facts into helpful insight and understanding. We’re providing this use case as an illustration, but it does not imply that the same conclusions can be made in similar cases. We will be happy to discuss it, however, as well as how the particulars of this case might be transferable to your situation—so don’t hesitate to contact us! Also, please be aware that we do sometimes use automatic translations, which might slightly distort the information.